我省第一条完全国产化车轮智能生产线全面达产达效
太原新闻网 2022/11/14
11月12日,太重集团轨道公司10月份生产成绩单出炉,截至10月31日,太重轨道车轮一厂智能化升级改造项目单月生产车轮25584件,这标志着我省唯一一条完全国产化车轮智能生产线全面达产达效。这条生产线的车轮锻造量从实现单小时、24小时、72小时理论设计产能,再到单月生产车轮能力完全达标,仅用了90天时间。
车轮一厂智能化升级改造项目的顺利完成,离不开太重轨道人的齐心协力。该生产线10月份共计生产11个品种的车轮,部分品种数量不足1000件,这意味着每生产一种车轮,不到24小时就需要全线更换一次模具,这给单月实现25000件车轮的目标增加了很大难度。太重轨道成立了“全面达产达效攻关组”,小组提前根据生产计划合理安排工装、模具及测量工具等配套加工计划,倒排进度,时间表精确到小时,确保单日产量保持在800件以上。在生产批量产品时,生产、设备及技术组通力协作,增加有效生产时间,确保单日产量保持在900件以上。全体领导班子成员带领部门负责人和设备技术人员,执行24小时值班工作制,任何负责区域发生故障,负责人必须连续跟班,直到修复为止。叉车实行机动倒班制,确保产品及时输出。各生产小组对可能发生的各类突发情况制定预案,至少2套方案,以确保第一时间恢复生产。10月初,我市多地实行区域静默管理,为了把疫情对生产的影响降到最低,即使能回家的职工也主动放弃回家,轮流上岗,确保产线连续产出车轮。
在智能化升级改造项目达产达效的同时,太重轨道公司还通过一系列技术改造,实现降本增效。车轮在锻造前需进行除鳞(去除钢坯表面氧化皮)工艺,这个过程中液压控制系统的故障率很高,成为制约生产效率再提高的瓶颈。班组人员想方设法优化液压系统,通过改变除鳞水泵频率来实现对高压、低压水的控制,改进后故障率降幅超10%。课题攻关组还通过给环形炉运送钢锭的小车增加缓冲装置,延长了轴承使用寿命,降低故障率,每月减少因更换轴承停机时长约30个小时,单月节省燃气费用超6万元。同时,班组自主设计的炉底排炉渣系统,不仅大大降低了劳动强度,还减少了环形炉的停机时间,每月节省人工成本超5000元。
扫描上面二维码
手机看资讯
加入城市买房砍价群,实时讨论购房热点话题

获取楼盘信息

进群聊房
- 相关阅读
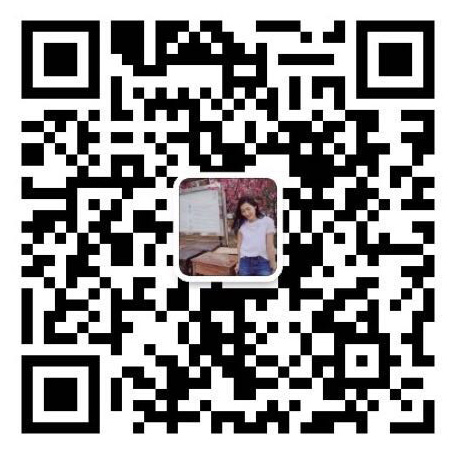
加入买房砍价群
- 讨论购房话题
- 你问我答
- 专业讲解
- 全面分析
今日热点要闻